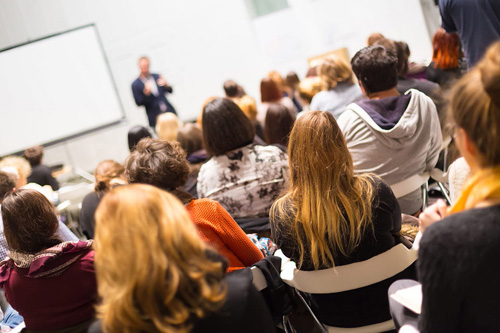
一填空題
1.冷沖壓的優(yōu)點有: 生產(chǎn)率高、操作簡便,尺寸穩(wěn)定、互換性好,材料利用率高 。
2.冷沖壓是利用安裝在壓力機上的 模具 對材料 施加壓力 ,使其產(chǎn)生 分離或塑性變形 ,從而獲得所需零件的一種加工方法。
3.一般的金屬材料在冷塑變形時會引起材料性能的變化。隨著變形程度的增加,所有的強度、硬度都 提高 ,同時塑性指標 降低 ,這種現(xiàn)象稱為冷作硬化。
4.拉深時變形程度以 拉深系數(shù)m 表示,其值越小,變形程度越 大 。
5.材料的屈強比 小 ,均勻延伸率 大 有利于成形極限的提高。
6.沖裁件的斷面分為 圓角,光面,毛面,毛刺 四個區(qū)域。
7.翻孔件的變形程度用 翻孔系數(shù)K 表示,變形程度最大時,口部可能出現(xiàn) 開裂
8.縮孔變形區(qū)的應力性質為 雙向壓縮應力 ,其可能產(chǎn)生的質量問題是 失穩(wěn)起皺
9.精沖時沖裁變形區(qū)的材料處于 三向壓應力 ,并且由于采用了 極小 的間隙,沖裁件尺寸精度可達IT8-IT6級。
10.冷沖壓模具是實現(xiàn)冷沖壓工藝的一種 工藝裝備 。
11.落料和沖孔屬于 分離工序 ,拉深和彎曲屬于 成形工序 。
12.變形溫度對金屬塑性的影響很大,一般來說,隨著變形溫度的升高,塑性 提高 ,變形抗力 降低 。
13.壓力機的標稱壓力是指滑塊在 離下止點前 某一特定位置時,滑塊上所容許承受的 最大作用力 。
14.材料在塑性變形中,變形前的體積 等于 變形后的體積,用公式來表示即: ε1+ε2+ε3=0 。
15.沖裁的變形過程分為 彈性變形 , 塑性變形 , 斷裂分離 三個階段。
16.沖裁模工作零件刃口尺寸計算時,落料以 凹模 為基準,沖孔以 凸模 為基準,凸模和凹模的制造精度比工件高 2-3級 。
17.沖裁件之間及沖裁件與條料側邊之間留下的余料稱作 搭邊 。它能補償條料送進時的定位誤差和下料誤差,確保 沖出合格的制件 。
18.彎曲零件的尺寸與模具工作零件尺寸不一致是由于 彎曲回彈而引起的 ,校正彎曲比自由彎曲時零件的尺寸精度 要高 。
19.拉深時可能產(chǎn)生的質量問題是 起皺和開裂
20在室溫下,利用安裝在壓力機上的模具對被沖材料施加一定的壓力,使之產(chǎn)生分離和塑性變形,從而獲得所需要形狀和尺寸的零件(也稱制件)的一種加工方法。
21用于實現(xiàn)冷沖壓工藝的一種工藝裝備稱為沖壓模具。
22沖壓工藝分為兩大類,一類叫分離工序,一類是變形工序。
23物體在外力作用下會產(chǎn)生變形,若外力去除以后,物體并不能完全恢復自己的原有形狀和尺寸,稱為塑性變形。
24變形溫度對金屬的塑性有重大影響。就大多數(shù)金屬而言,其總的趨勢是:隨著溫度的升高,塑性增加,變形抗力降低。
25以主應力表示點的應力狀態(tài)稱為主應力狀態(tài),表示主應力個數(shù)及其符號的簡圖稱為主應力圖??赡艹霈F(xiàn)的主應力圖共有九種。
26塑性變形時的體積不變定律用公式來表示為:ε1+ε2+ε3=0。
27加工硬化是指一般常用的金屬材料,隨著塑性變形程度的增加,其強度、硬度和變形抗力逐漸增加,而塑性和韌性逐漸降低。
28在實際沖壓時,分離或成形后的沖壓件的形狀和尺寸與模具工作部分形狀和尺寸不盡相同,就是因卸載規(guī)律引起的彈性回復(簡稱回彈)造成的。
29材料對各種沖壓成形方法的適應能力稱為材料的沖壓成形性能。沖壓成形性能是一個綜合性的概念,它涉及的因素很多,但就其主要內(nèi)容來看,有兩個方面:一是成形極限,二是成形質量。
30 B23-63表示壓力機的標稱壓力為 630KN 。其工作機構為曲柄連桿滑塊機構。
31 32-300是一種 液壓機 類型的壓力機。
32 在沖壓工作中,為頂出卡在上模中的制件或廢料,壓力機上裝有可調(diào)剛性頂件(或稱打件)裝置。
33 離合器與制動器是用來控制曲柄滑塊機構的運動和停止的兩個部件。
曲柄壓力機的標稱壓力是指滑塊在離下死點前某一特定距離時,滑塊上所容許承受的最大作用力。5. 沖壓生產(chǎn)中,需要將板料剪切成條料,這是由剪切機來完成的。這一工序在沖壓工藝中稱下料工序。
34 圓形墊圈的內(nèi)孔屬于 沖孔 外形屬于 落料 。
35 沖裁斷面分為四個區(qū)域:分別是 塌角 , 光面 , 毛面 , 毛刺 。
36 沖裁過程可分為 彈性變形 , 塑性變形 , 斷裂分離 三個變形階段。
37 工作零件刃口尺寸的確定沖孔以凸 模為計算基準,落料以凹 模為計算基準。
38 沖裁件的經(jīng)濟沖裁精度為 IT11級 。
39 凸凹模在下模部分的叫 倒裝式復合模 ,凸凹模在上模部分的叫 正裝式復合模 ,其中 正 裝 式 復合模多一套打件裝置。
40 彈性卸料裝置除了起卸料作用外,還起壓 料作用,它一般用于材料厚度較小的情況。
41 側刃常用于 級進模 中,起 控制條料送進步距 的作用。
42 沖壓力合力的作用點稱為 模具的壓力中心 ,設計模具時,要使 壓力中心 與模柄中心重合。
10.擋料銷用于條料送進時的粗定位,導正銷用于條料送進時的精定位。
43 將各種金屬坯料沿直線彎成一定 角度 和 曲率 ,從而得到一定形狀和零件尺寸的沖壓工序稱為彎曲。
44 彎曲時外側材料受拉伸,當外側的拉伸應力超過材料的抗拉強度以后,在板料的外側將產(chǎn)生裂紋,此中現(xiàn)象稱為 彎裂 。
45 在外荷作用下,材料產(chǎn)生塑性變形的同時,伴隨彈性變形,當外荷去掉以后,彈性變形恢復,使制件的 形狀 和 尺寸 都發(fā)生了變化,這種現(xiàn)象稱為回彈。
46 在彎曲過程中,坯料沿凹模邊緣滑動時受到摩擦阻力的作用,當坯料各邊受到 摩擦阻力 不等時,坯料會沿其長度方向產(chǎn)生滑移,從而使彎曲后的零件兩直邊長度不符合圖樣要求,這種現(xiàn)象稱之為 偏移 。
47 為了確定彎曲前毛坯的 形狀 和 大小 ,需要計算彎曲件的展開尺寸。
48 彎曲件的工藝安排使在 工藝分析 和 計算 之后進行的一項設計工作。
49 常見的彎曲模類型有: 單工序彎曲模、級進彎曲模 、 復合彎曲模 、通用彎曲模 。
50 對于小批量生產(chǎn)和試制生產(chǎn)的彎曲件,因為生產(chǎn)量小,品種多,尺寸經(jīng)常改變,采用常用的彎曲模成本高,周期長,采用手工時強度大,精度不易保證,所有生產(chǎn)中常采用 通用彎曲模 。
51 凹模圓角半徑的大小對彎曲變型力, 模具壽命 ,彎曲件質量 等均有影響。
52 對于有壓料的自由彎曲,壓力機公稱壓力為 F壓 機≥(1.6~1.8)(F自+FY) 。
32 用拉深模將一定形狀的平面坯料或空心件制成開口件的沖壓工序叫做 拉深 。
53 一般情況下,拉深件的尺寸精度應在 IT13 級以下,不宜高出 IT11 級。
54 實踐證明,拉深件的平均厚度與坯料厚度相差不大,由于塑性變形前后體積不變,因此,可以按 坯料面積等于拉深件表面積 原則確定坯料尺寸。
55 為了提高工藝穩(wěn)定性,提高零件質量,必須采用稍大于極限值的 拉深系數(shù) 。
56 窄凸緣圓筒形狀零件的拉深,為了使凸緣容易成形,在拉深窄凸緣圓筒零件的最后兩道工序可采 用 錐形凹模 和 錐形壓料圈 進行拉深。
57 壓料力的作用為: 防止拉深過程中坯料起皺
58 目前采用的壓料裝置有 彈性壓料 和 剛性壓料 裝置。
59 軸對稱曲面形狀包括 球形件 , 拋物線形件 , 錐形件 。
60 在拉深過程中,由于板料因塑性變形而產(chǎn)生較大的加工硬化,致使繼續(xù)變形苦難甚至不可能。為可后繼拉深或其他工序的順利進行,或消除工件的內(nèi)應力,必要時進行 工序間 熱處理或 最后消除應力 的熱處理。
61 在沖壓過程中,清洗的方法一般采用 酸洗 。為了降低冷沖壓模具與坯料的摩擦力,應對坯料進 表面處理 和 潤滑處理 。
62冷積壓模具一般采用 可調(diào)試冷擠壓模 和 通用擠壓模 。
63翻邊按變形性質可分為 伸長類翻邊 和 壓縮類翻邊 。
64在沖壓過程中,脹形分 平板坯料 的局部凸起脹形和 立體空心 的脹形。
65壓制加強筋時,所需沖壓力計算公式為: F=LtσbK 。
66把不平整的工件放入模具內(nèi)壓平的工序叫 校平 。
67冷擠壓的尺寸公差一般可達到 IT7 。
68 空心坯料脹形 是將空心工序件或管狀毛坯沿徑向往外擴張的沖壓工序。
69徑向積壓又稱橫向擠壓,即積壓時,金屬流動方向與凸緣運動方向 垂直 。
70 覆蓋件 是指覆蓋車類發(fā)動機、底盤、駕駛室和車身的薄板異型類表面零件和內(nèi)部零件。
71為了實現(xiàn)覆蓋件拉深,需要制件以外增加部分材料,而在后續(xù)工序中又將去切除,這部分增補的材料稱為 工藝補充部分 。
72利用 拉深筋 ,控制材料各方向留入凹模的阻力,防止拉深時因材料流動不均勻而發(fā)生起皺和破裂,是覆蓋件工藝設計和模具設計的特點和重要內(nèi)容。
73確定覆蓋件的切邊方向必須注意 定位要方便可靠 和 要保證良好的刃口強度 這兩點。
74覆蓋件翻邊質量的好壞和翻邊位置的準確度,將直接影響汽車車身的 裝配精度 和 質量 。
75 覆蓋件的工序工件圖 是指拉深工件圖、切邊工件圖及翻邊工件圖等工序件圖,是模具設計過程中貫徹工藝設計圖、確定模具結構及尺寸的重要依據(jù)。
76覆蓋件拉深模結構與拉深使用的壓力機有很大的關系,可分為 單動拉深模、 多為雙動拉深模 和 雙動拉深模 。
77拉深筋的作用是增大或調(diào)節(jié)拉深時坯料各部分的變形阻力,控制材料流入,提高穩(wěn)定性,增大制件的剛度,避免 起皺 和 破裂 現(xiàn)象。
78 工藝孔 是為了生產(chǎn)和制造過程的需要,在工藝上增設的孔,而非產(chǎn)品制件上需要的孔。
79覆蓋件的翻邊包括兩個方面:一是 輪廓外形翻邊 ,二是 窗口封閉內(nèi)形翻邊 。
80在模具的工作部分分布若干個等距工位,在每個每個工位上設置了一定沖壓工序,條料沿模具逐工位依次沖壓后,在最后工位上從條料中便可沖出一個合格的制件來的模具叫 級進模 。
81多工位級進模按主要工序分,可分為 級進沖裁模 、 級進彎曲模 、 級進拉深模 。
82多工位級進模按組合方式分,可分為 落料彎曲級進模 、 沖裁翻邊級進模 、 沖裁拉深級進模 、 翻邊拉深級進模 。
83衡量排樣設計的好壞主要看 工序安排是否合理 ,能否保證 沖件的質量并使沖壓過程正常穩(wěn)定進行 ,模具結構是否 簡單,制造維修是否方便 ,是否符合制造和使用單位的習慣和實際條件等等。
84進行工位設計就是為了確定模具工位的 數(shù)目 、各工位加工的 內(nèi)容 、及各工位沖壓工序的 順序 。
85對于嚴格要求的局部內(nèi)、外形及成組的孔,應考慮在同一工位上沖出,以保證位置精度 。
86如何處理好相關部件幾次沖裁產(chǎn)生的 相接問題 ,將直接影響沖壓件的質量。
87在多工位級進模內(nèi)條料送進過程中,會不斷得被切除余料,但在各工位之間達到最后工位以前,總要保留一些材料將其連接起來,以保證條料連續(xù)的送進,這部分材料稱為 載體 。
88級進模中卸料板的另一個重要作用是 保護細小的凸模 。
89對于自動送料裝置的多工位級進模應采用 自動檢測保護裝置 。
90模具因為磨損和其他原因而失效,最終不能修復而報廢之前所加工的沖件總數(shù)稱為 模具壽命 。
91模具經(jīng)過一定時間的使用,由于種種原因不能再沖出合格的沖件產(chǎn)品,同時又不能修復的現(xiàn)象稱為 失效 。
92沖模一般零件選用材料是應具有一定的 力學 性能和 機械加工 性能。
93在實際生產(chǎn)中,由于沖壓件材料厚度公差較大,材料性能波動,表面質量差不干凈等,將造成模具工作零件 磨損加劇 . 和 崩刃 。
94對于一定條件下的模具鋼,為了提高起耐磨性,需要在硬度高的機體上分布有 細小堅硬的碳化物 。
95低淬透性冷作模具鋼他包括 碳素工具鋼 和 部分低合金工具鋼 。
96 材料的耐磨性 將直接影響模具零件的使用壽命和沖件質量。
97鋼結硬質合金的可鑄性和可加工性較差,因而對 鑄造溫度 和 鑄造方法 以及切削加工范圍都有嚴格的要求。
98不同沖壓模具對材料的性能要求不同,拉深等成形模要求有 高耐磨性 和 高黏附性 。
100. 硬質合金鋼與鋼結硬質合金性能相比具有 硬度高 和 模具使用壽命長 等特點。
四 問答、計算題
1.冷沖壓的特點?
答:(1) 便于實現(xiàn)自動化,生產(chǎn)率高,操作簡便。大批量生產(chǎn)時,成本較低。
(2) 冷沖壓生產(chǎn)加工出來的制件尺寸穩(wěn)定、精度較高、互換性好。
(3) 能獲得其它加工方法難以加工或無法加工的、形狀復雜的零件。
(4) 冷沖壓是一種少無切削的加工方法,材料利用率較高,零件強度、剛度好。
2.冷沖壓的基本工序?
答:分離工序和變形工序。
分離工序:材料所受力超過材料的強度極限,分離工序的目的是使沖壓件與板料沿一定的輪廓線相互分離,成為所需成品的形狀及尺寸。
成形工序:材料所受力超過材料的屈服極限而小于材料的強度極限,成形工序的目的,是使沖壓毛坯在不破壞的條件下發(fā)生塑性變形,成為所要求的成品形狀和尺寸。
3.板平面方向性系數(shù)?
答:板料經(jīng)軋制后晶粒沿軋制方向被拉長,雜質和偏析物也會定向分布,形成纖維組織,使得平行于纖維方向和垂直于纖維方向材料的力學性能不同,因此在板平面上存在各向異性,其程度一般用板厚方向性系數(shù)在幾個特殊方向上的平均差值Δr(稱為板平面方向性系數(shù))。Δr值越大,則方向性越明顯,對沖壓成形性能的影響也越大。
4.沖壓成形性能?
答:材料對各種沖壓成形方法的適應能力。沖壓成形性能包括兩個方面:一是成形極限,二是成形質量。
材料沖壓成形性能良好的標志是:材料的延伸率大,屈強比小,屈彈比小,板厚方向性r大,板平面方向性Δr值小。
5.沖壓對材料的基本要求為:具有良好的沖壓成形性能,如成形工序應具有良好的塑性(均勻伸長率δj高),屈強比σs/σb和屈彈比σs/E小,板厚方向性系數(shù)r大,板平面方向性系數(shù)Δr小。具有較高的表面質量,材料的表面應光潔平整,無氧化皮、裂紋、銹斑、劃傷、分層等缺陷。厚度公差應符合國家標準。
6.如何選擇壓力機?
答:主要包括類型選擇和規(guī)格兩個方面。
(1)類型選擇 沖壓設備類型較多,其剛度、精度、用途各不相同,應根據(jù)沖壓工藝的性質、生產(chǎn)批量、模具大小、制件精度等正確選用。一般生產(chǎn)批量較大的中小制件多選用操作方便、生產(chǎn)效率高的開式曲柄壓力機。但如生產(chǎn)洗衣桶這樣的深拉伸件,最好選用有拉伸墊的拉伸油壓機。而生產(chǎn)汽車覆蓋件則最好選用工作臺面寬大的閉式雙動壓力機。
(2)規(guī)格選擇 確定壓力機的規(guī)格時要遵循如下原則:
① 壓力機的公稱壓力必須大于沖壓工藝力。但對工作行程較長的工序,不僅僅是只要滿足工藝力的大小就可以了,必須同時考慮滿足其工作負荷曲線才行。
②壓力機滑塊行程應滿足制件在高度上能獲得所需尺寸,并在沖壓工序完成后能順利地從模具上取出來。對于拉伸件,則行程應在制件高度兩倍以上。
③壓力機的行程次數(shù)應符合生產(chǎn)率的要求。
④壓力機的閉合高度、工作臺面尺寸、滑塊尺寸、模柄孔尺寸等都要能滿足模具的正確安裝要求,對于曲柄壓力機,模具的閉合高度應在壓力機的最大裝模高度與最小裝模高度之間。工作臺尺寸一般應大于模具下模座50-70mm(單邊),以便于安裝,墊板孔徑應大于制件或廢料投影尺寸,以便于漏料模柄尺寸應與模柄孔尺寸相符。
7.什么是壓力機的裝模高度,與壓力機的封閉高度有何區(qū)別?
答:壓力機的裝模高度是指滑塊在下死點時,滑塊下表面到工作墊板上表面的距離。當裝模高度調(diào)節(jié)裝置將滑塊調(diào)整至最上位置時(即連桿調(diào)至最短時),裝模高度達到最大值,稱為最大裝模高度;裝模高度調(diào)節(jié)裝置所能調(diào)節(jié)的距離,稱為裝模高度調(diào)節(jié)量。和裝模高度并行的標準還有封閉高度。所謂封閉高度是指滑塊在下死點時,滑塊下表面到工作臺上表面的距離。它和裝模高度之差恰好是墊板的高度。因為模具通常不直接裝在工作臺面上,而是裝在墊板上,所以裝模高度用得更普遍。
8.什么是沖裁間隙?為什么說沖裁間隙是重要的。
答: 凸模與凹模工作部分的尺寸之差稱為間隙。沖裁模間隙都是指的雙面間隙。間隙值用字母Z表示。間隙之所以重要,體現(xiàn)在以下幾個方面:
1)沖裁間隙對沖裁件質量的影響
(1)間隙對斷面質量的影響 模具間隙合理時,凸模與凹模處的裂紋(上下裂紋)在沖壓過程中相遇并重合,此時斷面塌角較小,光面所占比例較寬,毛刺較小,容易去除。斷面質量較好;
如果間隙過大,凸模刃口處的裂紋較合理間隙時向內(nèi)錯開一段距離,上下裂紋未重合部分的材料將受很大的拉伸作用而產(chǎn)生撕裂,使塌角增大,毛面增寬,光面減少,毛刺肥而長,難以去除,斷面質量較差;
間隙過小時,凸模與凹模刃口處的裂紋較合理間隙時向外錯開一段距離上下裂紋中間的一部分材料,隨著沖裁的進行將進行二次剪切,從而使斷面上產(chǎn)生二個光面,并且,由于間隙的減小而使材料受擠壓的成分增大,毛面及塌角都減少,毛刺變少,斷面質量最好。因此,對于普通沖裁來說,確定正確的沖裁間隙是控制斷面質量的一個關鍵。
(2) 沖裁間隙對尺寸精度的影響 材料在沖裁過程中會產(chǎn)生各種變形,從而在沖裁結束后,會產(chǎn)生回彈,使制件的尺寸不同于凹模和凸模刃口尺寸。其結果,有的使制件尺寸變大,有的則減小。其一般規(guī)律是間隙小時,落料件尺寸大于凹模尺寸,沖出的孔徑小于凸模尺寸;間隙大時,落料件尺寸小于凹模尺寸,沖出的孔徑大于凸模尺寸。
2)沖裁間隙對沖壓力的影響
一般來說,在正常沖裁情況下,間隙對沖裁力的影響并不大,但間隙對卸料力、推件力的影響卻較大。間隙較大時,卸料及推料時所需要克服的摩擦阻力小,從凸模上卸料或從凹模內(nèi)推料都較為容易,當單邊間隙大到15%~20%料厚時,卸料力幾乎等于零。
3) 沖裁間隙對沖模壽命的影響
由于沖裁時,凸模與凹模之間,材料與模具之間都存在摩擦。而間隙的大小則直接影響到摩擦的大小。間隙越小,摩擦造成的磨損越嚴重,模具壽命就越短,而較大的間隙,可使摩擦造成的磨損減少,從而提高了模具的壽命。
9.比較單工序模、復合模、級進模的優(yōu)缺點。
答: 各種類型模具對比見下表
模具種類 對比項目 | 單工序模 | 級進模 | 復合模 | |
無導向的 | 有導向的 | |||
制件精度 | 低 | 一般 | 可達IT13-IT8 | 可達IT9-IT8 |
制件形狀尺寸 | 尺寸大 | 中小型尺寸 | 復雜及極小制件 | 受模具結構與強度制約 |
生產(chǎn)效率 | 低 | 較低 | 最高 | 一般 |
模具制造工作量和成本 | 低 | 比無導向的略高 | 沖裁較簡單制件時比復合模低 | 沖制復雜制件時比連續(xù)模低 |
操作的安全性 | 不安全,需采取安全措施 | 較安全 | 不安全,需采取安全措施 | |
自動化的可能性 | 不能使用 | 最宜使用 | 一般不用 |